Die Casting: The Ultimate Guide
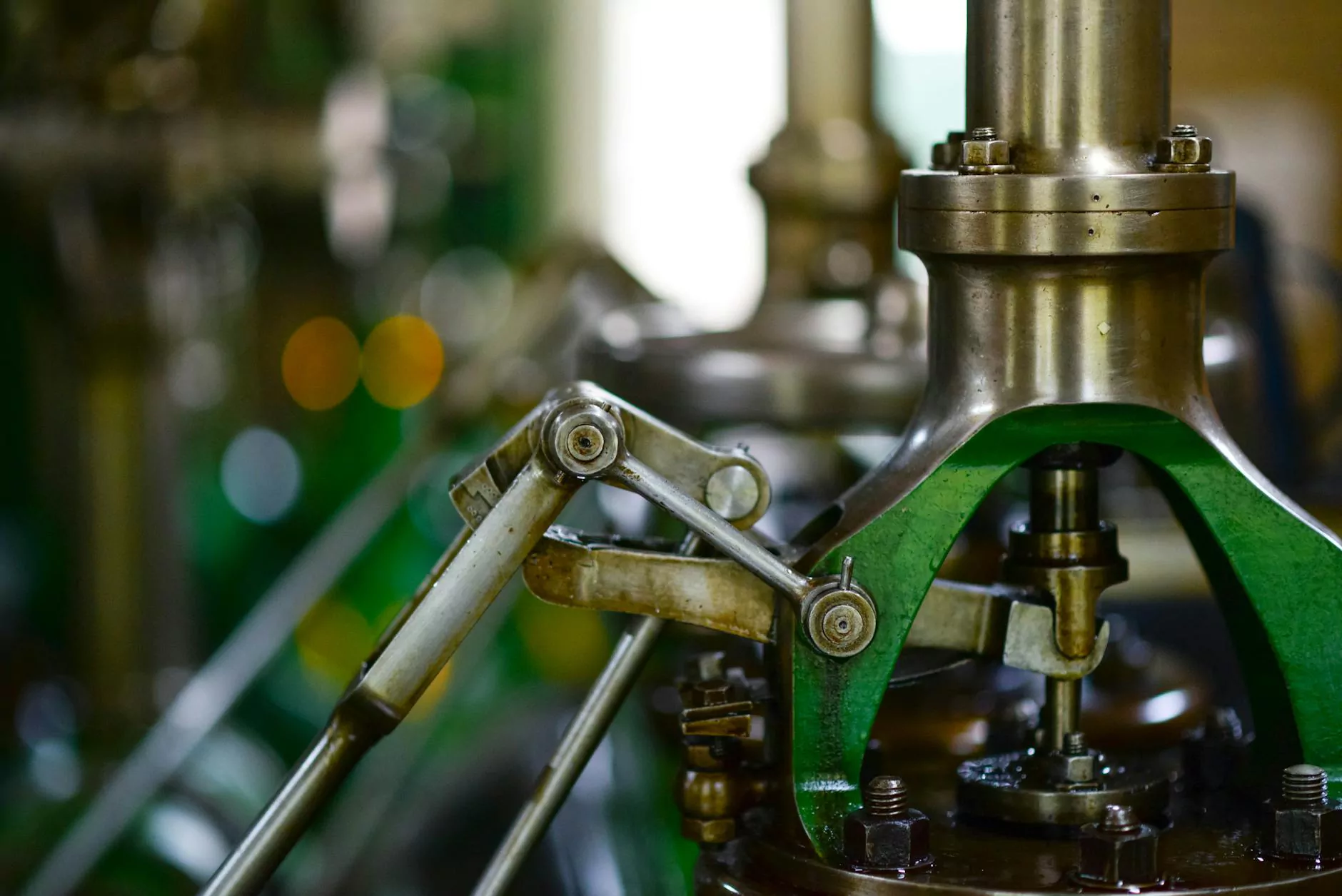
Introduction
Welcome to DeepMould.net, your go-to source for all your metal fabrication needs. In this article, we will explore the fascinating world of die casting. Whether you are new to the industry or seeking to expand your knowledge, we have you covered. Let's dive in!
What is Die Casting?
Die casting is an efficient and versatile metal fabrication process that involves injecting molten metal into a reusable mold or die. The molten metal is forced under high pressure, filling intricate cavities within the die to create a precise and accurate final product. This process is widely used in various industries, including automotive, aerospace, electronics, and more.
Benefits of Die Casting
DeepMould.net, as leading metal fabricators specializing in die casting, offers top-quality services with numerous advantages. Let's explore some of the key benefits:
1. High Precision and Accuracy
Die casting provides exceptional precision and accuracy, making it an ideal choice for producing complex shapes with tight tolerances. The advanced mold design and high-pressure injection result in consistent and repeatable parts, ensuring minimal variation and excellent dimensional control.
2. Excellent Surface Finish
The die casting process produces parts with a superior surface finish, often eliminating the need for additional post-processing. The high-pressure injection ensures smooth and detailed features, reducing the time and cost associated with secondary finishing operations.
3. Rapid Production
DeepMould.net understands the importance of efficiency in today's fast-paced business environment. With die casting, high-volume production can be achieved within a short time frame. The quick cycle times and rapid solidification of the molten metal allow for faster output, enabling you to meet strict project deadlines.
4. Design Flexibility
Die casting offers exceptional design flexibility, allowing for the creation of intricate and complex geometries. The process enables the incorporation of thin walls, fine details, and undercuts, resulting in lightweight yet robust parts. With various metals available, including aluminum, zinc, and magnesium, you have the freedom to choose the optimal material for your application.
5. Cost-Effective Solution
By leveraging the benefits of die casting, you can achieve cost savings in multiple ways. The high production efficiency reduces labor costs, while the excellent dimensional control minimizes the need for rework or scrap. The tooling costs for die casting may be higher initially, but the longevity and reusability of the molds make it a cost-effective solution in the long run.
The Die Casting Process
The die casting process consists of several steps, each playing a crucial role in ensuring the quality of the final product:
1. Mold Preparation
Prior to casting, the mold or die needs to be properly prepared. This includes lubricating the surfaces, ensuring they are clean and free from debris, and aligning the halves of the mold accurately.
2. Melting and Injection
Once the mold is ready, the selected metal alloy is melted in a furnace. The molten metal is then injected into the mold under high pressure, filling the cavities and forming the desired shape.
3. Cooling and Solidification
After injection, the molten metal rapidly cools and solidifies within the mold. The cooling time is carefully controlled to ensure optimal properties and minimize defects.
4. Ejection and Finishing
Once the cooling process is complete, the solidified part is ejected from the mold. Any excess material, such as flash or overflow, is removed, and additional finishing processes, such as trimming or surface treatment, can be performed if required.
Applications of Die Casting
The versatility of die casting allows it to be used in various industries and applications. Some common examples include:
- Automotive components: Engine parts, transmission cases, and chassis components benefit from the strength and lightweight characteristics of die-cast parts.
- Electronics: Die casting is utilized in producing enclosures, heat sinks, and connectors for electronic devices, ensuring optimal performance and protection.
- Aerospace: Critical aerospace components, such as turbine blades and structural parts, often require the high precision and strength that die casting offers.
- Appliances: Many household appliances, such as refrigerators, washing machines, and air conditioners, contain die-cast parts for durability and aesthetic appeal.
Conclusion
DeepMould.net, the leading metal fabricators specializing in die casting, offers unparalleled expertise, advanced technology, and exceptional quality to meet your business needs. With the numerous benefits of die casting, including high precision, excellent surface finish, rapid production, design flexibility, and cost-effectiveness, it is clear why this process is widely adopted across industries. Embrace the advantages of die casting with DeepMould.net today and take your business to new heights!