The Importance of Injection Molding Machine Components
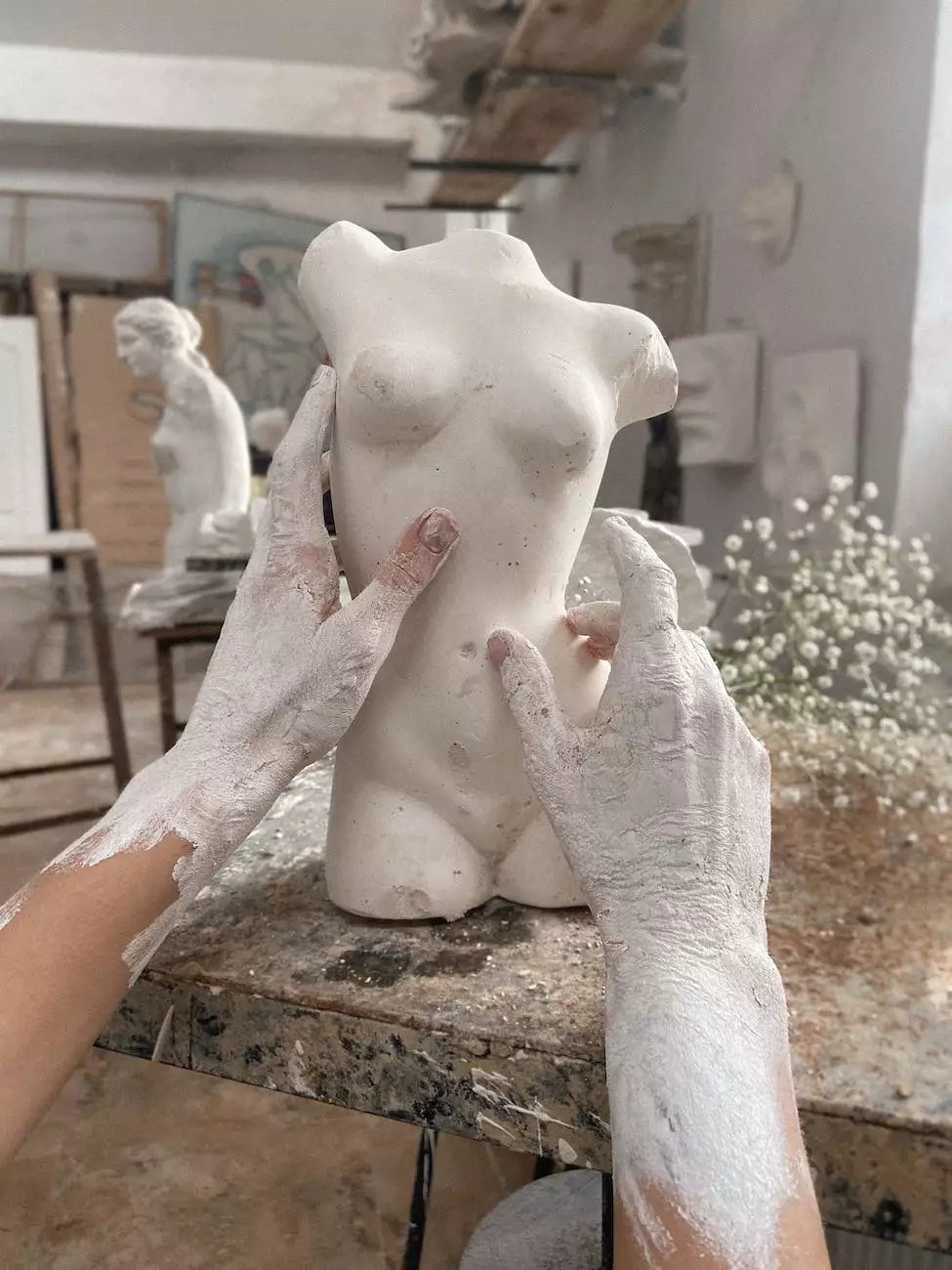
In the field of injection molding, the success of any manufacturing process heavily relies on the quality and efficiency of the injection molding machine components. These components, such as molds, barrels, heaters, nozzles, clamps, platens, ejectors, valves, screws, pumps, hydraulics, electronics, control systems, and automation, work in harmony to ensure accurate and consistent production.
Molds: The Crucial Building Blocks
At the heart of every injection molding machine lies the mold. This vital component determines the final shape and structure of the product being manufactured. Molds are typically made from durable materials like steel and can be customized based on specific product requirements. Injection molds consist of two halves, referred to as the core and the cavity, which form the desired shape when closed together.
High precision molds are essential for creating products with intricate designs and complex geometries. These molds undergo thorough engineering and design processes to ensure optimal functionality. By utilizing state-of-the-art technology, advanced CAD/CAM software, and meticulous machining techniques, reputable metal fabricators like QuickParts can deliver top-notch molds that result in superior final products.
Barrels and Heaters: Precise Temperature Control
An integral part of the injection molding process is the barrel and heater combination. The barrel is responsible for melting the raw material, usually in the form of pellets or granules, and maintaining it at the proper temperature for injection. The heater ensures accurate and consistent heat levels within the barrel for optimal material flow and quality.
Manufacturers like QuickParts understand the significance of precise temperature control to avoid issues such as material degradation and inconsistency in molding. By employing advanced heating technology and temperature monitoring systems, they ensure that the desired temperature profiles are maintained consistently throughout the entire injection process.
Nozzles and Clamps: Controlling Material Flow and Stability
Nozzles are responsible for injecting the molten material from the barrel into the mold cavity. They play a critical role in controlling material flow and preventing leaks or air gaps in the final product. The design and quality of the nozzle greatly influence the molding process and the performance of the finished part.
Clamps are another essential component of injection molding machines. They secure the mold in place during the injection process, preventing any unwanted movement or shifting. The clamps ensure that the mold remains tightly closed, maintaining precision and consistency in the final product.
Platens: Applying the Right Amount of Pressure
The platens in an injection molding machine provide the necessary force to keep the mold closed. They apply pressure to ensure that the molten material fills the mold completely and evenly, resulting in high-quality parts with minimal defects. Proper platen design and functionality are critical to achieving consistent and accurate results in the injection molding process.
Ejectors and Valves: Releasing and Controlling the Parts
Ejectors are responsible for pushing the finished parts out of the mold once the injection and cooling processes are complete. They ensure the smooth release of the parts, preventing any damage or distortion that may occur during removal. Well-designed ejector systems contribute to efficient production cycles and faster turnaround times.
Valves play a key role in controlling the flow of materials and fluids within the injection molding machine. They regulate the amount of material being injected into the mold, ensuring precise measurements and minimizing waste. Expertly engineered valves allow for accurate control over every aspect of the injection process, contributing to consistent part quality.
Screws, Pumps, and Hydraulics: Efficient Material Handling
The screw, pump, and hydraulic systems work together to facilitate the efficient handling of the material during the injection molding process. The screw precisely meters the raw material, melts it, and injects it into the mold. The pump provides the necessary pressure and controls the flow of hydraulic oil, ensuring smooth machine operation. Hydraulics power the clamps, ejectors, and other machine movements, contributing to overall functionality and speed.
Electronics, Control Systems, and Automation: Precision and Efficiency
Modern injection molding machines incorporate electronics, control systems, and automation to achieve the highest levels of precision and efficiency. These components allow for precise control over temperature, pressure, injection speed, and cycle times, resulting in consistent and repeatable production.
The integration of automation technology further enhances the injection molding process by reducing human error and increasing productivity. Automated systems can handle tasks such as part removal, mold changes, and quality inspections, allowing operators to focus on higher-value activities.
Conclusion
Injection molding machine components form the backbone of the manufacturing process, dictating the quality, accuracy, and efficiency of the final product. From molds and barrels to heaters, nozzles, clamps, platens, ejectors, valves, screws, pumps, hydraulics, electronics, control systems, and automation, each component plays a crucial role in producing high-quality parts.
By partnering with reputable metal fabricators like QuickParts, businesses can ensure access to top-of-the-line injection molding machine components. These components contribute to optimized production cycles, reduced waste, and improved overall operational efficiency. With the right components in place, manufacturers can confidently meet the demands of the market and stay ahead of the competition.