Understanding Hydraulic Balls: A Key Component in Fittings
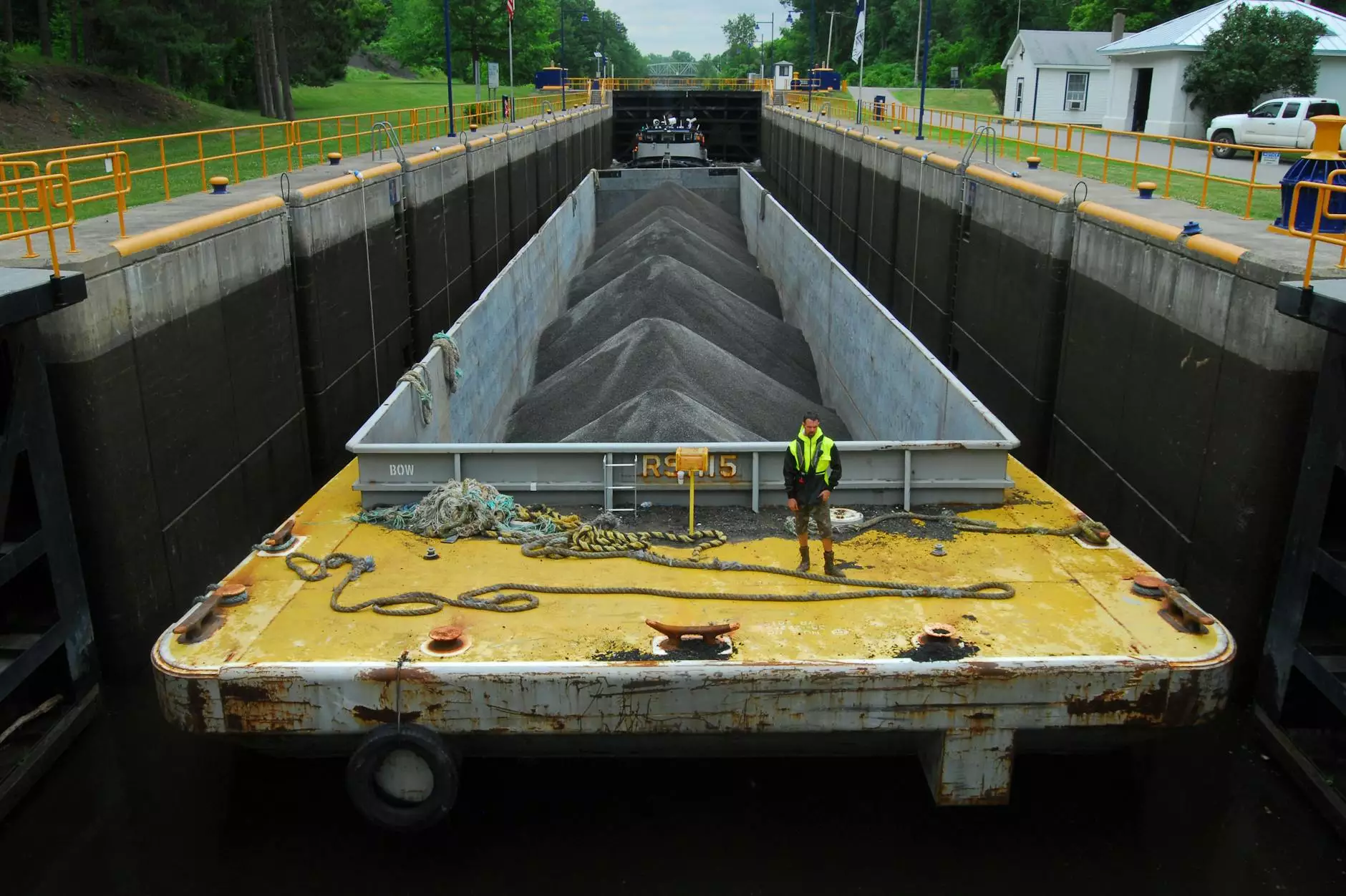
Hydraulic balls play a critical role in numerous mechanical and hydraulic systems, providing efficiency and reliability across various applications. This article aims to delve deep into the world of hydraulic balls, exploring their types, features, benefits, and applications within hydraulic fitting systems.
What are Hydraulic Balls?
Hydraulic balls are spherical components made from various materials including stainless steel, plastic, or other alloys designed to manage and regulate the flow of liquids within hydraulic systems. These balls are pivotal in functions such as sealing, controlling pressure, and providing flexibility in fluid transportation systems.
The Importance of Hydraulic Balls in Fittings
In hydraulic fittings, the use of hydraulic balls cannot be overstated. These components are central to ensuring that systems run smoothly and efficiently. Below are some reasons why hydraulic balls are essential:
- Sealing Capability: Hydraulic balls act as seals, preventing fluid leakage and maintaining pressure levels.
- Flow Control: They allow for precise regulation of fluid flow, ensuring optimal performance of hydraulic systems.
- Durability: Made from robust materials, hydraulic balls can withstand extreme pressure and temperatures, ensuring longevity.
- Reduced Maintenance Costs: Their reliability reduces the need for frequent maintenance and replacements, saving businesses time and money.
Types of Hydraulic Balls
Hydraulic balls come in various designs suited for different applications. Understanding these types is vital for selecting the right component for your needs:
1. Standard Hydraulic Balls
These are the most common type used in various applications, known for their basic functionality in sealing and flow control.
2. High-Pressure Hydraulic Balls
Designed for extreme conditions, high-pressure hydraulic balls are made from advanced materials that can withstand greater stress and strain.
3. Plastic Hydraulic Balls
For applications where metal may corrode, plastic hydraulic balls offer a lightweight alternative that prevents rusting and chemical damage.
4. Ball Check Valves
These hydraulic balls feature a unique design that allows fluid to flow in one direction while preventing backflow, critical for many hydraulic systems.
Applications of Hydraulic Balls in Industrial Settings
Hydraulic balls are integrated into numerous industrial settings, each leveraging their unique benefits for specific functions:
- Automotive Industry: Used in hydraulic brake systems and power steering units for effective fluid control.
- Manufacturing: Essential in hydraulic machines that require precision fluid management.
- Aerospace: Used in various hydraulic systems due to their robustness and reliability.
- Construction: Hydraulic balls ensure smooth operation of machinery like excavators and loaders, which rely on hydraulic power.
Benefits of Using Hydraulic Balls
The inclusion of hydraulic balls in your fittings brings a myriad of advantages that enhance the overall efficiency and effectiveness of hydraulic systems:
- Enhanced Performance: Hydraulic balls contribute to the smoother operation of systems by ensuring precise flow control.
- Cost Efficiency: Long-lasting components reduce the frequency of replacements, leading to lower operational costs.
- Versatility: Suitable for various applications, hydraulic balls are adaptable across many industries.
- Safety: The sealing properties of hydraulic balls minimize the risk of leaks, thereby increasing workplace safety.
Choosing the Right Hydraulic Ball for Your Needs
When selecting a hydraulic ball for your fittings, consider the following factors to ensure you make an informed decision:
1. Material
The material of the hydraulic ball is crucial for its performance and longevity. Common materials include stainless steel, plastic, and brass. Choose a material based on the intended pressure and environmental conditions.
2. Size
The diameter of the hydraulic ball must match the specifications of the fittings to ensure optimal sealing and performance.
3. Application Suitability
Determine the specific requirements of your application. Whether it’s a high-pressure system or a corrosive environment, selecting the right type of hydraulic ball is vital.
4. Brand Reputation
Opt for hydraulic balls from trusted manufacturers known for quality and reliability. For instance, fitsch.cn offers a range of top-quality fittings and hydraulic balls tailored to meet diverse needs.
Maintenance Practices for Hydraulic Balls
To ensure the longevity and efficiency of hydraulic balls within your systems, consider implementing the following maintenance practices:
- Regular Inspections: Conduct routine checks for signs of wear or corrosion and replace any compromised components.
- Fluid Quality Monitoring: Ensure that the hydraulic fluids used are clean and compatible with the materials of the hydraulic balls.
- Seal Checks: Regularly check the sealing properties of hydraulic balls to maintain system integrity.
Future Trends in Hydraulic Ball Technology
The field of hydraulic technology is ever-evolving. Future trends may include:
- Improved Materials: Advancements in material science may yield even more durable and lightweight options for hydraulic balls.
- Smart Technology: Integration of sensors into hydraulic systems for real-time monitoring and adjustments.
- Sustainable Practices: Increased focus on eco-friendly materials and processes in the production of hydraulic balls.
Conclusion
In conclusion, hydraulic balls are a fundamental component of hydraulic fittings, driving efficiency and reliability across numerous applications. By understanding their functions, benefits, and maintenance practices, industries can optimize their hydraulic systems for enhanced performance. For high-quality fittings and hydraulic balls tailored to your specific needs, visit fitsch.cn today. Make informed choices that lead to improved operational success and business growth.