Unlocking the Potential of Plastic Injection Mold Companies
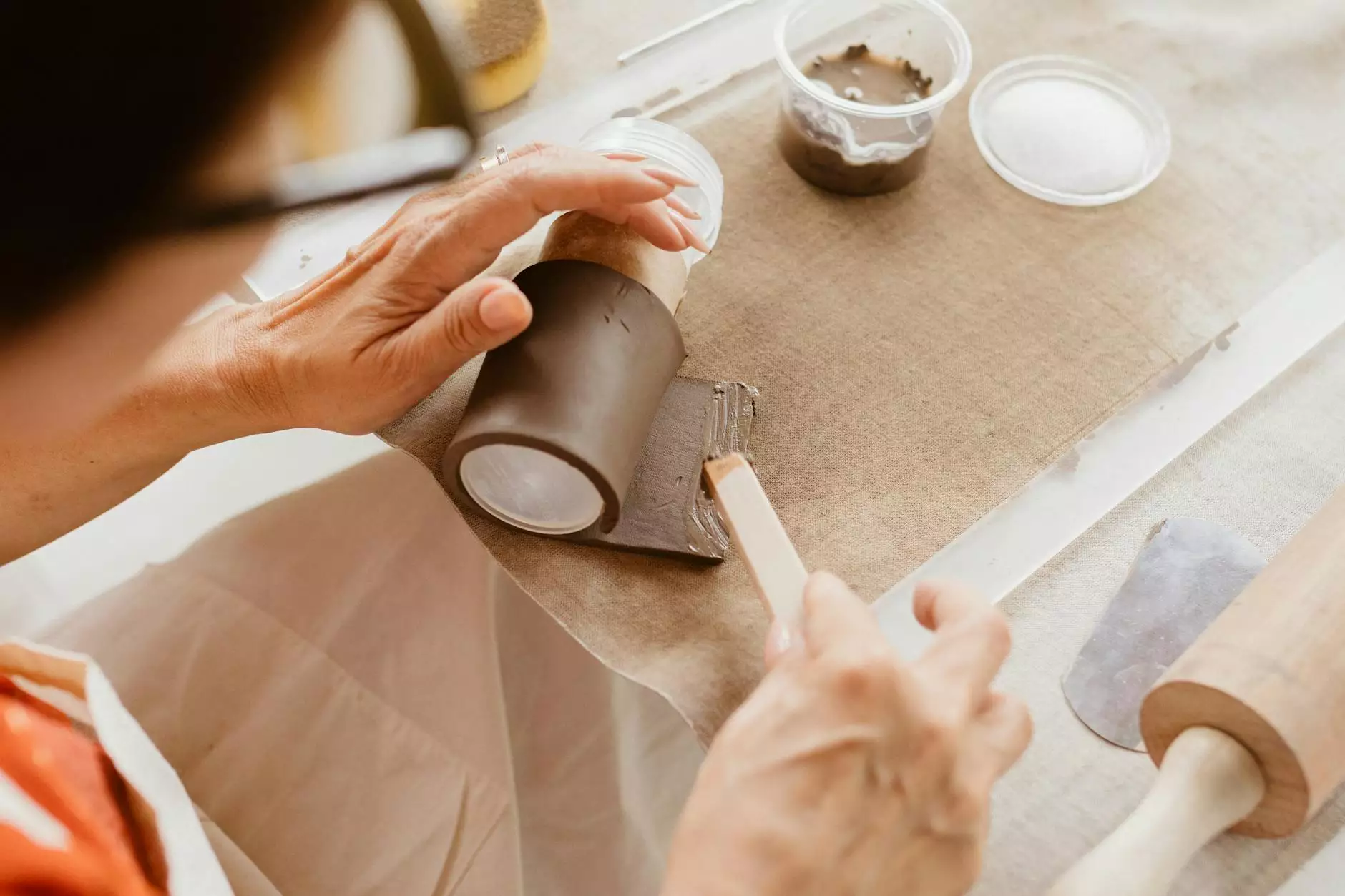
The manufacturing industry has seen incredible advancements over the years, with one of the most significant being the rise of plastic injection mold companies. These companies play a crucial role in producing high-quality plastic products that are essential in various industries. This article will delve into the intricacies of plastic injection molding, the advantages it offers, and how industry leaders like Deep Mould are setting standards in metal fabrication and mold design.
What is Plastic Injection Molding?
At its core, plastic injection molding is a manufacturing process used to create plastic parts by injecting molten plastic into a mold. The process is highly efficient and allows for the production of complex geometries with high precision. Here's a breakdown of the key components involved in this method:
- Mold Design: The mold is a critical element in the injection molding process. It is typically made from metal and is engineered to the specific shape required for the final product.
- Injection Unit: This component is responsible for melting the plastic and injecting it into the mold at high temperatures and pressures.
- Clamping Unit: After the mold is filled, it must be held closed during the cooling process. The clamping unit applies the necessary force to keep the mold from opening before the plastic has set.
These components work together seamlessly to produce high volumes of accurate and consistent plastic parts, making plastic injection molding one of the most popular manufacturing methods worldwide.
The Advantages of Plastic Injection Molding
There are numerous reasons why plastic injection mold companies are favored in manufacturing. Understanding these advantages can help businesses and individuals make informed decisions about their product development and production strategies. Here are some key benefits:
1. Cost-Effectiveness
One of the most appealing aspects of plastic injection molding is its cost-effectiveness for large production runs. The initial costs associated with creating molds can be high; however, once the molds are made, the cost per unit decreases significantly as production ramps up. This is crucial for businesses looking to scale efficiently.
2. High Precision and Quality
Plastic injection molding allows for high precision and repeatability. The molds are designed using advanced CAD software, ensuring that each part produced is identical. This level of precision is vital in industries where quality standards are stringent, such as in automotive and medical applications.
3. Design Versatility
With plastic injection molding, there is a vast array of materials that can be used to create parts, including thermoplastics, thermosets, and elastomers. Moreover, the process allows for complex designs that might not be possible with other manufacturing techniques. This versatility enables companies to innovate and create products that meet specific needs.
4. Efficient Production
Following the setup of molds, the injection molding process can produce large quantities of products in a relatively short timeframe. The automation of the process further enhances efficiency, reducing labor costs and minimizing human error.
Applications of Plastic Injection Molding
The applications of plastic injection molding span a diverse range of sectors. Here are some of the primary industries that benefit from this innovative manufacturing technique:
- Automotive: From dashboard components to exterior trim, the automotive industry relies heavily on plastic injection molding for lightweight and durable parts.
- Consumer Electronics: Many electronic devices utilize injection-molded plastic parts, providing essential protection and functionality.
- Medical Devices: Precision and reliability are fundamental in the medical field, making plastic injection molding a preferred manufacturing method for medical instruments and devices.
- Packaging: Injection molding is widely used in producing packaging solutions, such as containers and lids, which require high durability and safety.
The Role of Deep Mould in the Industry
Deep Mould has emerged as a leader among plastic injection mold companies, known for its commitment to quality and innovation. Based in the heart of the manufacturing hub, Deep Mould leverages cutting-edge technology to produce high-quality molds that meet the rigorous demands of today's industries.
Commitment to Quality
Quality assurance is at the forefront of Deep Mould's operations. Each project undergoes meticulous planning and execution, with state-of-the-art quality control processes in place to ensure that every mold produced meets or exceeds industry standards. This dedication to excellence has built a reputation that is recognized by clients globally.
Innovative Solutions
Deep Mould specializes in custom mold design and manufacturing, providing clients with unique solutions tailored to their specific needs. This bespoke approach ensures that businesses can count on them for innovative products that can differentiate their offerings in the marketplace.
Sustainability Practices
In an age where environmental concerns are paramount, Deep Mould has adopted sustainable practices in its operations. By prioritizing eco-friendly materials and minimizing waste during production, the company contributes positively to the environment while still meeting consumer demands.